How Does PUR Laminating Compare to Solvent-Based Lamination in Terms of Cost?


In today’s competitive manufacturing environment, choosing the right lamination method is essential for balancing product quality and operational cost. Two common technologies used in the lamination of films, foils, and papers are Polyurethane Reactive (PUR) laminating and solvent-based lamination. Both processes have unique advantages, but when it comes to cost-efficiency, the choice is not always clear-cut.
Overview of PUR and Solvent-Based Lamination
PUR Laminating uses a moisture-reactive polyurethane adhesive that cures when it reacts with moisture in the air or substrate. It is known for forming strong, flexible bonds and is widely used for high-performance applications, such as bookbinding, automotive interiors, furniture laminates, and flexible packaging.
Solvent-Based Lamination, on the other hand, involves the application of adhesives that are dissolved in solvents. Once applied, the solvents evaporate through heating, leaving behind a bond. This method has long been used in packaging, labels, and graphic arts.
Initial Equipment Investment
When comparing both technologies, PUR laminating systems generally require a higher upfront investment. This is because PUR adhesives are moisture-sensitive and require specialized equipment:
PUR systems need precise temperature control units, sealed tanks, and nitrogen blanketing to prevent premature curing.
Equipment must be designed to handle reactive adhesives, which adds to complexity and cost.
In contrast, solvent-based lamination lines have been in use for decades and are often less expensive to purchase, especially second-hand systems. However, environmental regulations for handling solvents might necessitate the installation of ventilation systems, solvent recovery units, or explosion-proof components, which can significantly increase the initial investment.
Operational Costs
1. Energy Consumption
Solvent-based systems often require higher energy input to heat ovens for solvent evaporation and to maintain proper air ventilation. These ovens consume a large amount of electricity or gas, adding to operational costs.
PUR lamination, by contrast, uses lower heat, and often shorter drying times, which translates into reduced energy consumption over time.
2. Adhesive Usage and Efficiency
PUR adhesives, though more expensive per kilogram than solvent-based adhesives, are used more efficiently. They require a thinner application layer, and the strength of the bond often eliminates the need for over-application.
Solvent-based adhesives typically require higher coat weights and more waste, especially when machines start up or change jobs.
3. Labor and Handling
PUR systems require trained operators due to the reactive nature of the adhesive. This may increase initial training costs.
Solvent-based systems are generally simpler to operate, but require more frequent cleaning due to adhesive build-up and solvent residue, adding to downtime and labor hours.
Maintenance and Safety Costs
PUR adhesives, once cured, are extremely difficult to remove. This means that:
Equipment must be cleaned regularly with dedicated PUR cleaning agents to avoid solidification inside hoses and nozzles.
Maintenance schedules must be strictly followed, which may involve higher cost for specialized cleaning solutions and part replacements.
Solvent-based systems have their own challenges:
Solvent fumes pose health and fire risks, requiring ventilation systems, safety training, and compliance certifications.
Environmental regulations may require solvent recycling units or disposal services, adding indirect costs.
In many regions, regulatory compliance for solvent emissions is becoming more stringent. This could lead to fines or equipment upgrades, making solvent systems more expensive to operate in the long run.
Long-Term Cost and ROI
Despite higher initial costs, PUR laminating systems often offer a better ROI over time due to:
Reduced adhesive consumption
Lower energy usage
Improved bond strength and product durability, which reduces rework or returns
Faster line speeds due to shorter curing or drying times
Moreover, PUR laminated products tend to outperform solvent-based laminated products in terms of heat resistance, moisture barrier, and adhesion to difficult substrates, allowing manufacturers to enter premium markets and charge higher prices.
Hidden Costs to Consider
1. Environmental and Legal Compliance
Governments worldwide are tightening controls on VOCs (volatile organic compounds). Solvent-based systems release VOCs into the atmosphere, requiring:
Licensing
Regular inspections
Environmental reporting
All of these contribute to hidden compliance costs.
2. Product Differentiation
The superior finish and durability of PUR-laminated products often justify higher pricing in the market. Thus, PUR may offer better value-add potential despite slightly higher per-unit cost.
When comparing PUR laminating to solvent-based lamination from a cost perspective, it’s clear that the decision is not solely about material prices or equipment cost. Instead, it's a matter of total cost of ownership, which includes:
Equipment and installation
Energy and adhesive usage
Labor and maintenance
Safety and environmental compliance
Product quality and market value
Solvent-based lamination may seem cost-effective in the short term, especially for high-volume, low-margin applications in markets with relaxed regulations. However, PUR laminating offers long-term economic and performance benefits, particularly for manufacturers aiming for high-quality, sustainable, and regulatory-compliant solutions.
Ultimately, the best choice depends on your production scale, application type, target market, and long-term strategy. For manufacturers focused on innovation, durability, and environmental responsibility, investing in PUR laminating may prove to be the smarter economic decision in the years to come.
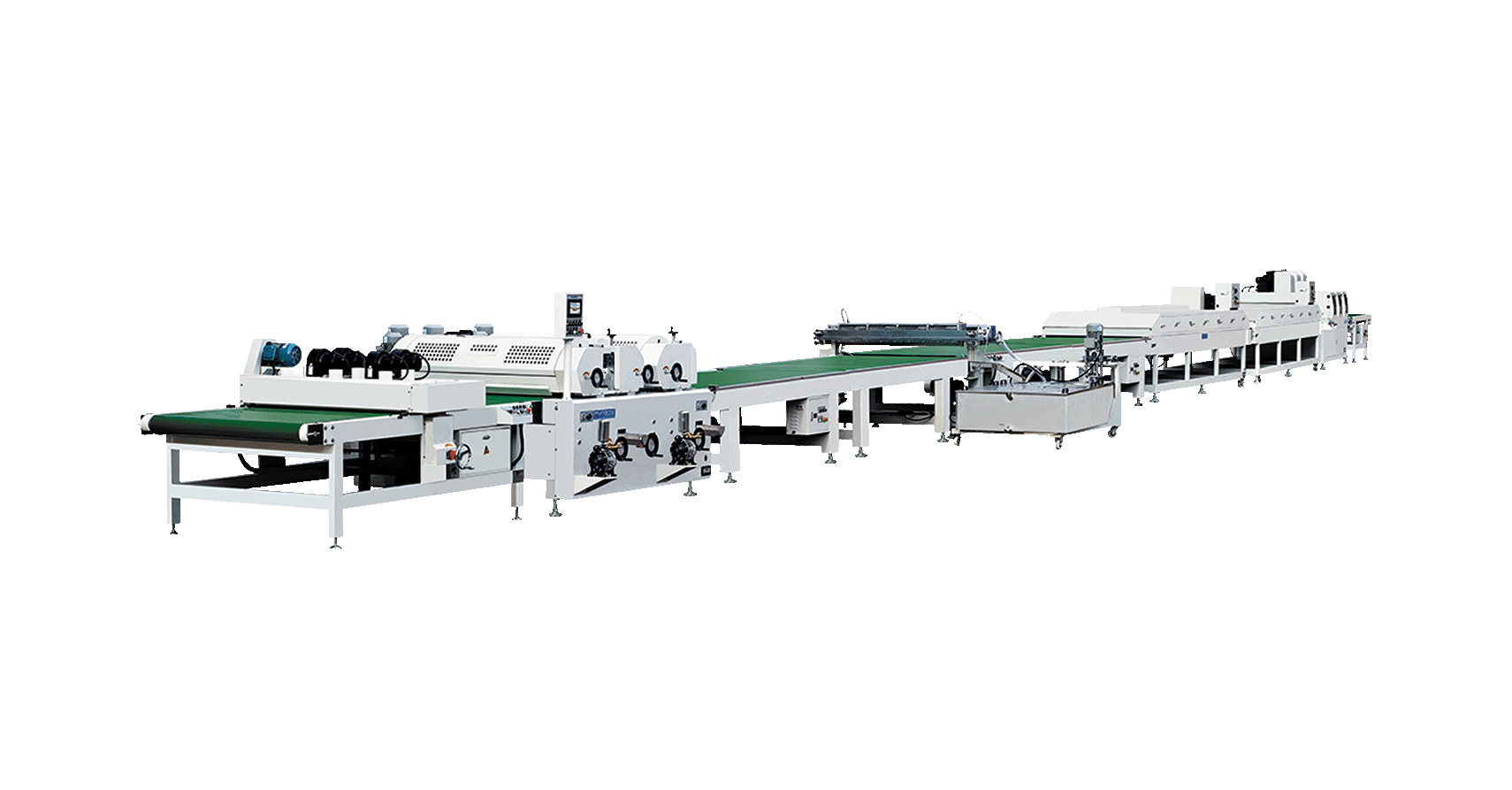


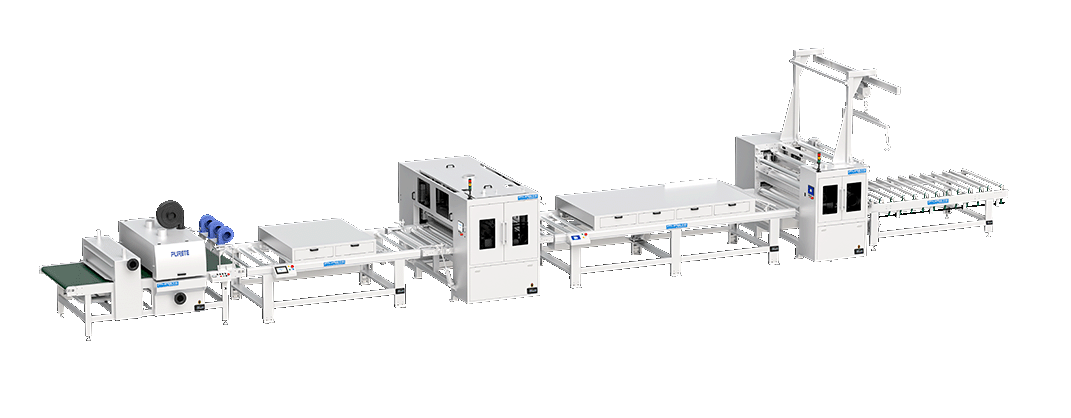
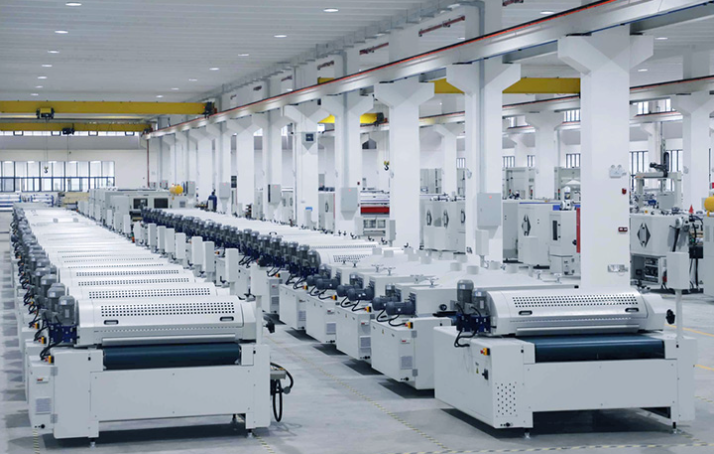
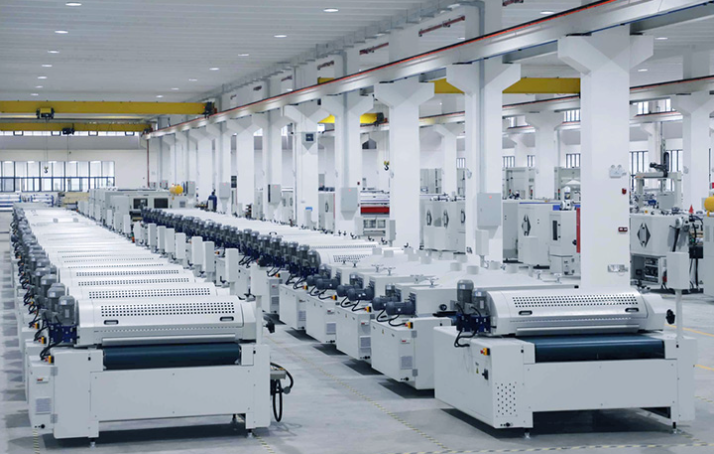

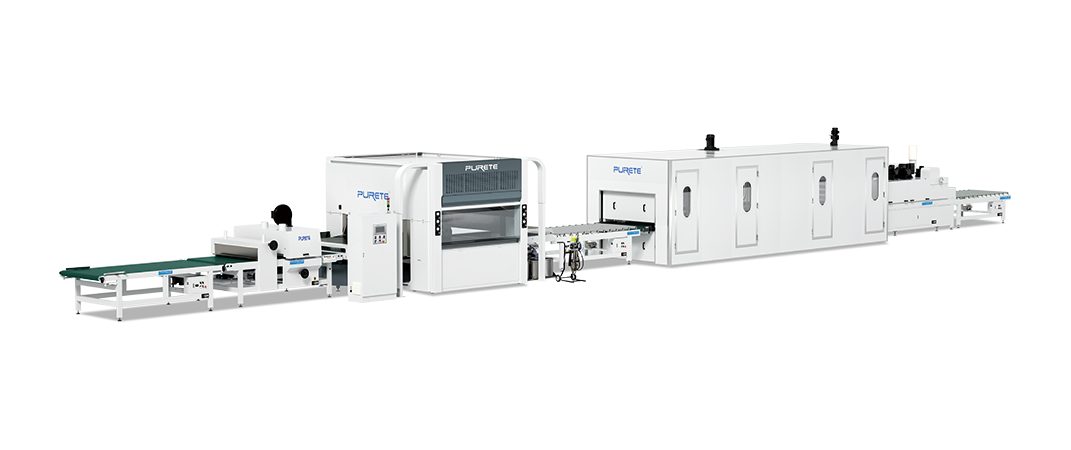