The Working Principle and Core Technologies of Intelligent Coating Machine Systems


With continuous advancements in industrial technology, intelligent Coating Machine Systems have become indispensable tools in modern manufacturing. Widely applied in industries such as electronics, automotive, aerospace, and medical devices, these systems significantly improve production efficiency, product quality, and environmental performance.
1. Working Principle of Intelligent Coating Machine Systems
The working principle of an intelligent coating system is based on modern automation control technology and precision spraying techniques. Real-time monitoring and feedback from multiple sensors enable intelligent management of the coating process. The main operational steps include:
Coating Supply and Preparation: The coating supply unit within the system mixes and prepares the coating materials according to predefined ratios, ensuring consistency and uniformity.
Spraying Control: High-precision spraying devices, such as electrostatic spray guns or aerosol nozzles, deliver micron-level precision during application. Spray paths and speeds are dynamically adjusted based on product shapes and material properties using intelligent algorithms.
Sensor Feedback and Adjustment: Throughout the spraying process, sensors such as infrared detectors and laser scanners monitor key parameters like coating thickness, surface uniformity, and material consumption. Feedback is sent to the control system, which automatically adjusts settings as needed.
Drying and Curing: After spraying, the system activates drying and curing devices, using infrared, ultraviolet, or hot air to ensure the coating forms quickly and adheres firmly.
2. Core Technologies of Intelligent Coating Machine Systems
The efficient operation of intelligent coating machine systems relies on several core technologies, which together enable the system to meet diverse industrial requirements.
(1) Automation Control Technology
Automation control forms the foundation of intelligent coating machine systems. Integrating technologies like PLC (Programmable Logic Controller) and SCADA (Supervisory Control and Data Acquisition), these systems achieve end-to-end automation, including coating supply, spray path planning, and parameter adjustments.
(2) Sensing and Data Analysis Technology
Multi-sensor integration is a highlight of intelligent coating machine systems. Sensors monitor critical parameters such as coating thickness, temperature, and humidity in real-time. Machine learning algorithms and data analysis enable the system to predict potential issues and make immediate corrections, ensuring high precision and consistency.
(3) Robotic Spraying Technology
Many intelligent coating machine systems utilize industrial robots for spraying tasks. Robotic spraying technology offers precise control over angles, distances, and speeds, making it especially suitable for complex surfaces and high-precision products.
(4) Electrostatic Coating Technology
Electrostatic coating technology uses electric fields to distribute coating particles evenly on surfaces. This method reduces material waste and enhances the adhesion and uniformity of the coating, making it a vital component of eco-friendly coating machine systems.
(5) Eco-Friendly and Energy-Saving Technologies
Modern intelligent coating machine systems incorporate eco-friendly technologies, such as the use of low-VOC (Volatile Organic Compounds) coatings, waste gas recovery devices, and intelligent energy management systems, minimizing environmental pollution and resource waste.
3. Advantages and Applications of Intelligent Coating Machine Systems
(1) Enhanced Production Efficiency
Traditional coating processes often require extensive manual intervention. Intelligent coating machine systems automate operations and intelligent adjustments, significantly reducing production cycles and labor costs.
(2) Improved Product Quality
Through precise spraying control and real-time feedback adjustments, these systems ensure uniform coating thickness and smooth surfaces, enhancing the product’s appearance and performance.
(3) Adaptability to Diverse Needs
Intelligent coating machine systems support highly customized solutions, accommodating various materials, sizes, and shapes. For instance, they are widely used for protective coatings on PCB boards in the electronics industry and for vehicle body and component coatings in the automotive sector.
(4) Significant Environmental Benefits
By optimizing coating material utilization and integrating waste gas recovery technologies, intelligent coating machine systems reduce environmental impact, aligning with green manufacturing practices.
4. Future Development Trends
With the rapid development of artificial intelligence, IoT, and 5G technologies, intelligent coating machine systems are advancing toward greater intelligence, connectivity, and sustainability. For example:
Predictive Maintenance: Big data analysis and predictive algorithms enable systems to identify potential equipment failures and notify users for maintenance in advance.
Cloud-Based Data Management: Coating process data can be uploaded to the cloud, enabling remote monitoring and optimization for enterprises.
Green Coating Solutions: Increased adoption of low-VOC and water-based coatings will further reduce environmental pressures.
Intelligent coating machine systems, with their efficiency, precision, and environmental friendliness, are revolutionizing traditional coating processes and injecting new vitality into the manufacturing industry. By integrating automation control, sensing technology, robotic spraying, and other core technologies, they meet diverse industrial needs while driving the industry toward intelligence and sustainability. In the future, intelligent coating machine systems will become essential tools for enhancing productivity and promoting sustainable development across various industries.
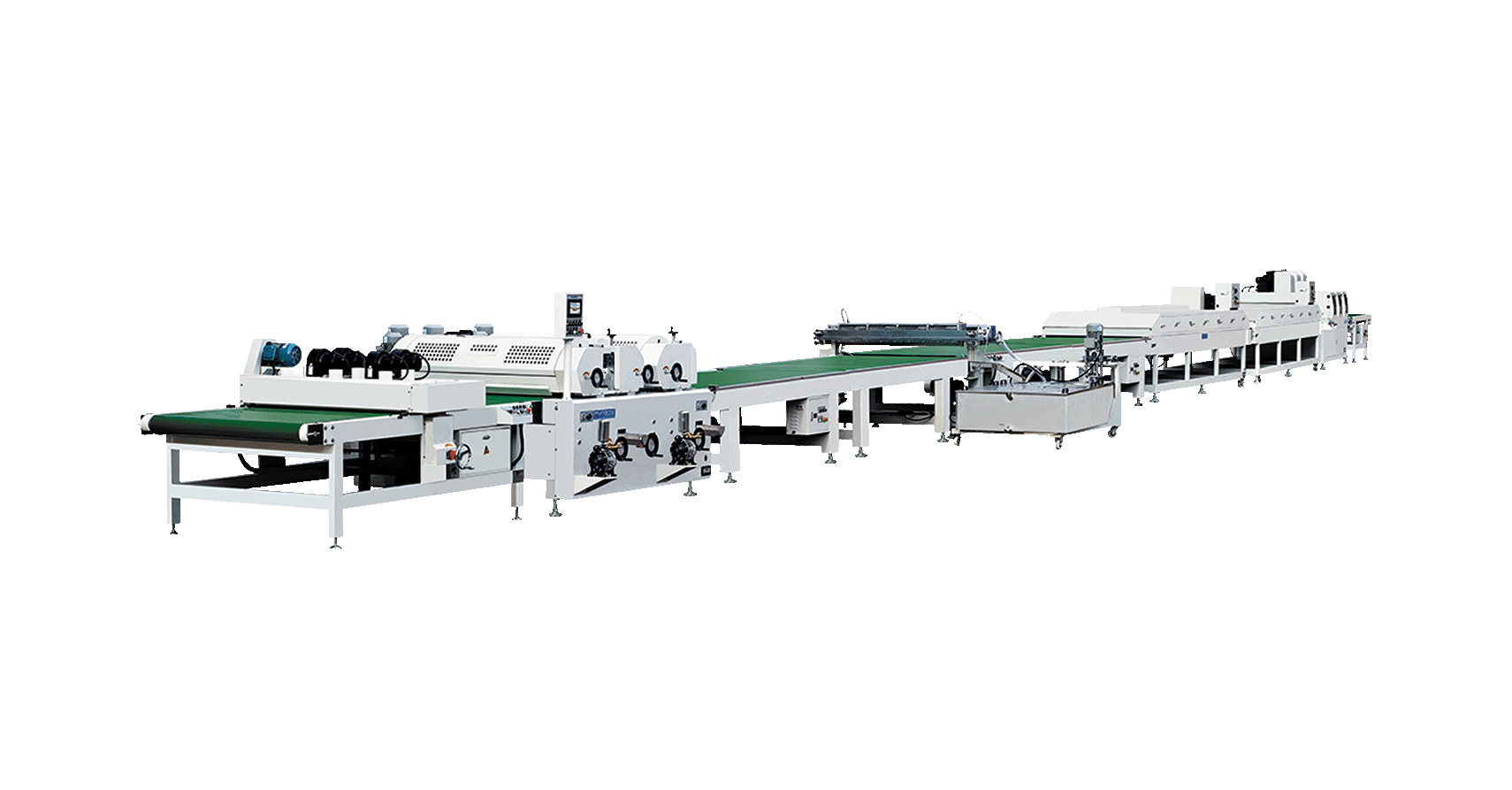


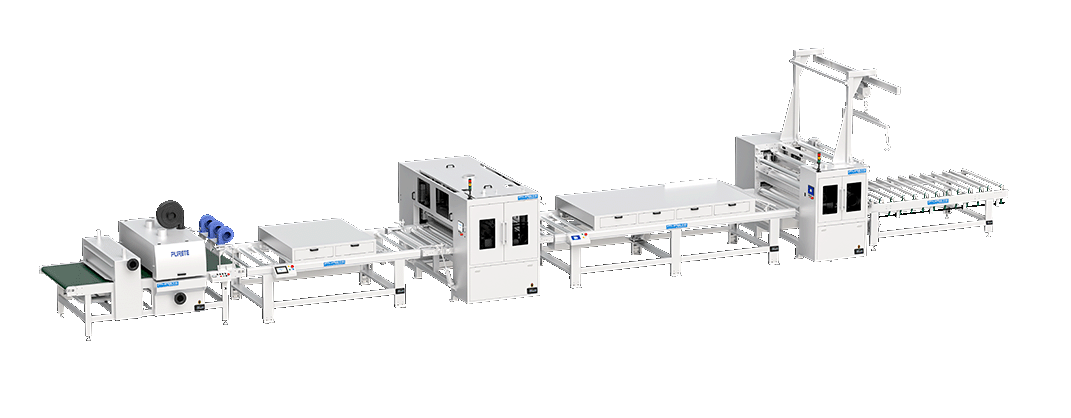
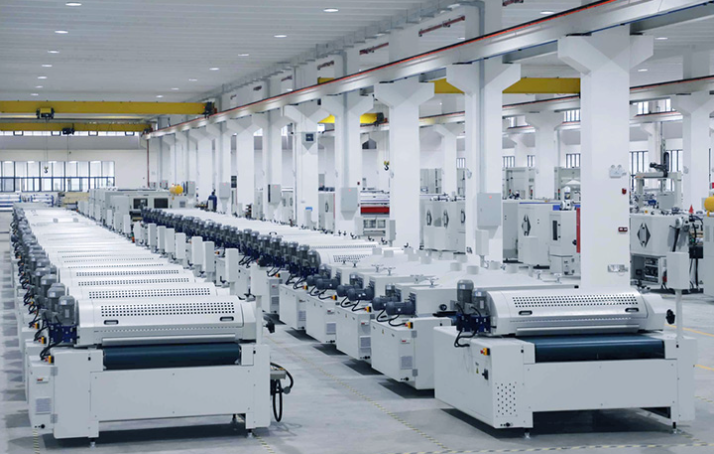
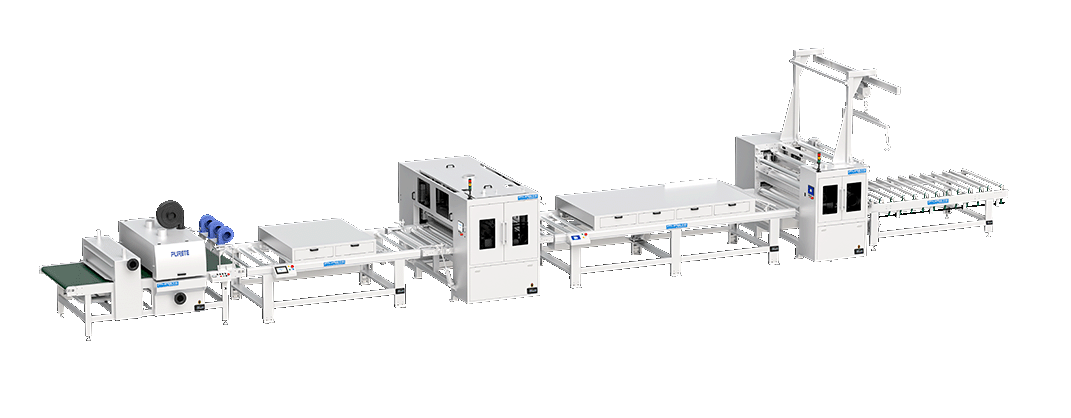
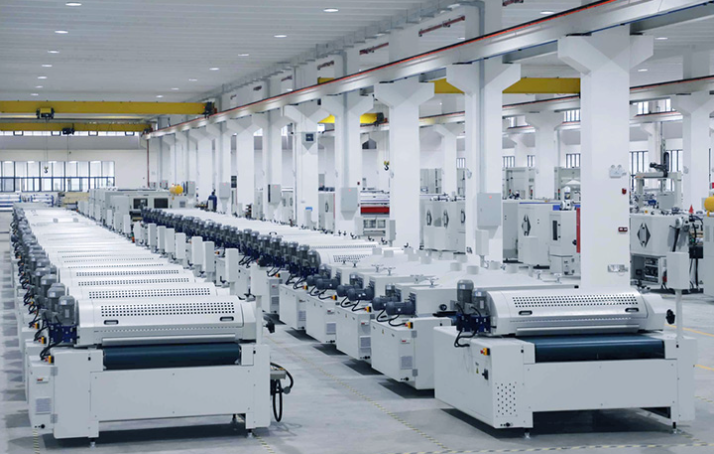
