How to Choose the Best PUR Laminating Machine for Your Production Line


Selecting the right PUR laminating machine is a critical decision that directly impacts your production efficiency, product quality, and long-term business success. As the manufacturing landscape evolves, PUR (Polyurethane Reactive) lamination technology has become the industry standard for high-value applications across furniture, construction, packaging, and decorative materials. However, with a variety of machines and configurations available, making an informed choice requires a thorough understanding of your production needs, technical requirements, and the unique advantages offered by PURETE's advanced PUR laminating solutions.
Assess Your Production Needs
Before investing in a new PUR laminating machine, conduct a comprehensive assessment of your production requirements. This foundational step ensures that your equipment aligns with both current and future business objectives.
Production Scale: Quantify your expected output—whether you handle large-scale continuous runs or smaller, highly customized batches. High-volume operations benefit from machines with greater automation and throughput, while flexible, modular systems are ideal for diversified or rapidly changing product lines.
Material Compatibility: Identify the core substrates in your workflow, such as MDF, melamine board, aluminum-plastic board, PVC, gypsum board, and metal. Also, consider the decorative films you intend to use, including PET, PVC, PP, paper, leather, acrylic, and more. PURETE's PUR laminating machines support a wide range of materials, enabling you to expand your product portfolio and serve multiple markets.
Product Specifications: Define the size, thickness, and surface finish required for your end products. This will influence the choice of machine width, roller configuration, and glue application system.
Application Areas: Different industries have unique demands. For example, construction and automotive sectors prioritize bonding strength and heat resistance, while the packaging industry may focus on speed and surface aesthetics. PURETE's machines are engineered to meet diverse application requirements.
Factory Environment: Evaluate your facility's ability to maintain the stable temperature and humidity conditions necessary for optimal PUR adhesive performance. Environmental stability is crucial for consistent lamination quality.
Key Factors to Consider When Choosing a PUR Lamination Machine
A high-performance PUR laminating machine is defined by several technical and operational parameters. Here's what to look for when selecting the best equipment for your production line:
Glue System and Control
PUR Glue Advantages: PUR adhesive is renowned for its superior bonding strength, flexibility, and resistance to heat, moisture, and chemicals. These properties make it ideal for demanding applications where durability and longevity are essential.
Glue Melting Speed: The efficiency of your production line depends on how quickly the machine can melt and supply PUR adhesive. PURETE machines are designed for rapid glue melting, ensuring uninterrupted operation and high throughput.
Precision Glue Application: Uniform and adjustable glue application is critical for achieving flawless lamination. Our machines feature advanced glue control systems that deliver consistent coverage, minimizing waste and ensuring product quality.
Temperature Control
Accurate Temperature Management: PUR adhesives are highly sensitive to temperature fluctuations. PURETE's laminating machines are equipped with precise, programmable temperature controls that maintain optimal adhesive performance, reduce the risk of defects, and enhance bonding strength.
Automation and Workflow Integration
Automation Level: Automation is key to reducing labor costs and increasing consistency. PURETE's PUR laminating machines offer features such as automatic substrate feeding, alignment, trimming, and cleaning. These systems streamline the production process, boost efficiency, and minimize manual intervention.
Roller and Pressing Systems: The choice between single and double roller configurations, as well as air or hydraulic pressure systems, affects lamination quality and adaptability to different materials. Our machines are engineered for maximum flexibility, allowing seamless transitions between product types.
Quick Changeover: In fast-paced production environments, minimizing downtime is essential. PURETE's quick-change roller systems enable rapid roller swaps—often in under two hours—supporting high-mix, low-volume manufacturing.
Equipment Stability and Reliability
Robust Machine Construction: Stability is the foundation of precision. PURETE's PUR laminating machines feature heavy-duty welded frames, such as 18mm steel plate structures, ensuring long-term durability and vibration-free operation.
Maintenance and Serviceability: Easy access to critical components for cleaning and maintenance reduces downtime and extends equipment lifespan. Our segmented bearing housings and external heat pipe systems simplify routine servicing and prevent common issues like glue leakage or burnout.
Dust and Static Control
Integrated Dust Removal: Clean substrates are essential for high-quality lamination. PURETE machines incorporate double-faced electrostatic and plasma-jet dust removal systems, effectively eliminating contaminants and ensuring a pristine bonding surface.
Cleanroom Compatibility: For industries requiring ultra-clean environments, our machines are compatible with cleanroom operations, further safeguarding product quality.
Customization and Scalability
Modular Design: As your business grows, your equipment should adapt. PURETE's modular laminating machines allow for future upgrades and the addition of optional modules, such as extra trimming, flipping, or cutting stations.
Material Versatility: Our machines are engineered to handle a broad spectrum of substrates and decorative films, enabling you to respond quickly to market trends and customer demands.
Energy Efficiency and Environmental Impact
Low VOC Emissions: PUR adhesives are more environmentally friendly than many traditional alternatives. PURETE's machines are designed for energy efficiency and minimal waste, supporting your sustainability goals.
Compact Footprint: Space is a valuable asset. Our laminating machines are optimized for high output in a compact design, maximizing your factory floor utilization.
Why Choose a PUR Lamination Machine From PURETE?
PURETE is committed to delivering industry-leading PUR laminating solutions that empower manufacturers to achieve superior results. Here's what sets our machines apart:
Unmatched Versatility: Our laminating lines are compatible with a vast array of materials, including PET, PETG, PP, PVC, CPL, HPL, acrylic, aluminum foil, SPC, and more. This flexibility ensures you can serve a wide range of industries and applications.
Precision Engineering: Every PURETE machine is built for accuracy and repeatability. Features like 0.02mm repeatable lifting precision and advanced glue spreaders guarantee consistent, high-quality lamination.
Operational Excellence: Our quick-change roller systems, automated workflow modules, and intelligent control interfaces streamline production, reduce labor, and maximize yield. User-friendly programming and parameter storage make recipe management effortless.
Maintenance Made Easy: Segmented bearing housings and external heat pipe systems facilitate easy maintenance and prevent common operational issues. Our machines are designed for reliability and long service life.
Tailored Solutions: We understand that every production line is unique. PURETE offers customized configurations to match your specific requirements, from machine size to workflow integration and optional modules.
Comprehensive Support: From installation and training to ongoing technical assistance, our team is dedicated to your success. We provide expert guidance at every stage, ensuring you get the most from your investment.
Proven Performance: Manufacturers worldwide trust PURETE for reliable, high-quality, and efficient PUR laminating solutions. Our machines are engineered for both sheet and roll materials, delivering minimal waste and high throughput.
Conclusion
Choosing the best PUR laminating machine for your production line is a strategic investment that requires careful consideration of your operational needs, material requirements, and long-term business goals. By focusing on advanced glue and temperature control, robust construction, automation, flexibility, and energy efficiency, you can ensure your production line remains competitive and future-ready.
PURETE's PUR laminating machines are designed to deliver exceptional performance, versatility, and reliability. As your trusted PUR laminating machine supplier, we are committed to helping you achieve outstanding product quality, operational efficiency, and sustainable growth. With the right equipment and support, your business can confidently meet the evolving demands of the market and secure long-term success.
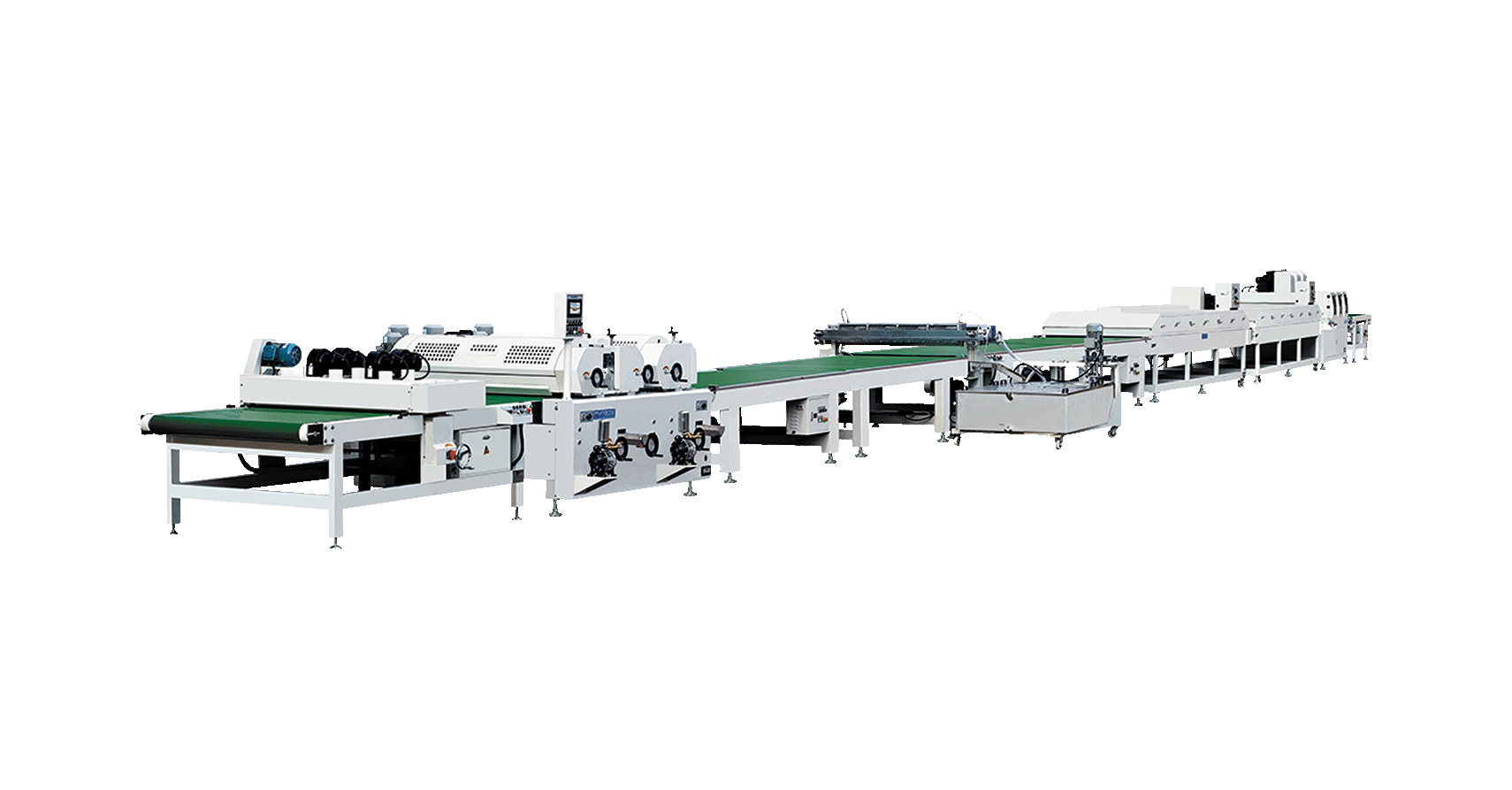


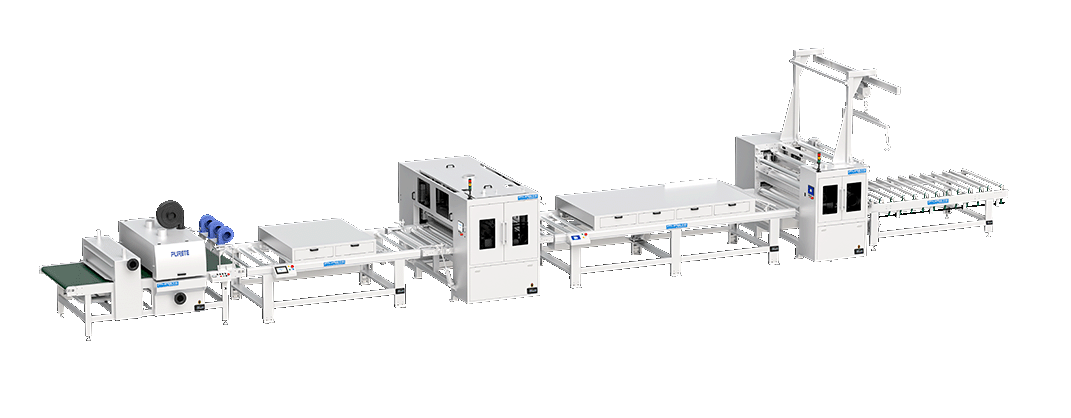
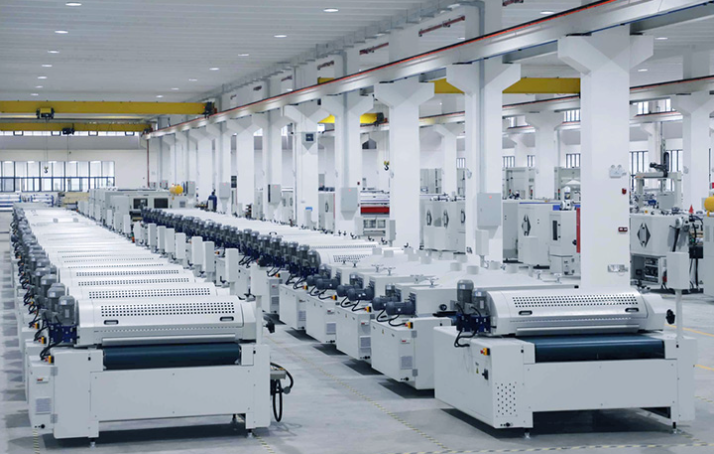
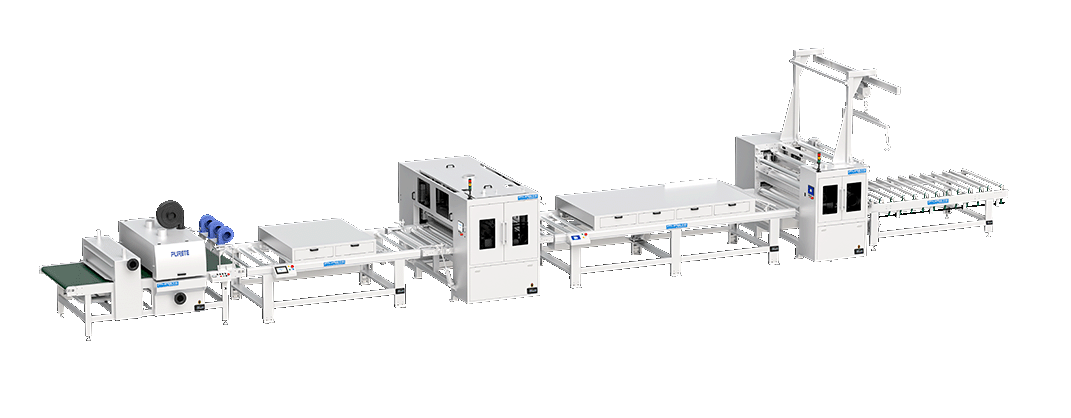
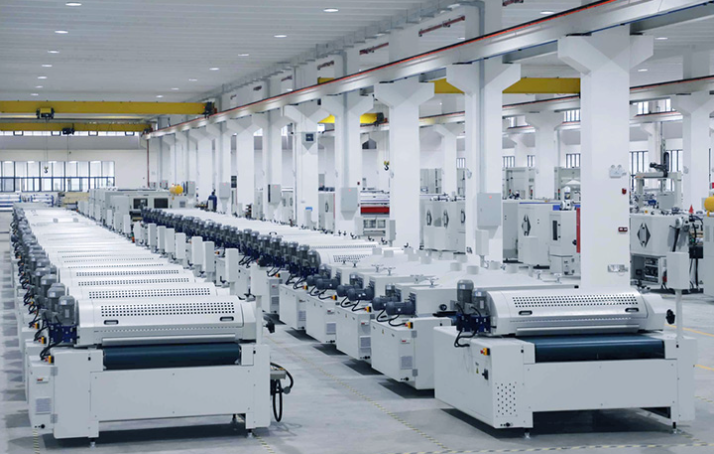
