How to Maintain and Clean Roller Coating Equipment for Optimal Performance


Roller coating equipment is a critical component in many manufacturing processes, particularly in industries like furniture, cabinetry, and metal finishing. Proper maintenance and cleaning of this equipment are essential to ensure consistent performance, extend its lifespan, and avoid costly downtime.
1. Daily Maintenance and Cleaning
Daily maintenance is crucial to prevent the buildup of coating materials and ensure smooth operation.
a. Clean the Rollers:
After each shift or production run, clean the rollers thoroughly to remove any residual coating material.
Use appropriate cleaning solvents recommended by the coating material manufacturer. For water-based coatings, water or mild detergents may suffice, while solvent-based coatings may require specific solvents.
Wipe the rollers with a lint-free cloth or use a roller cleaning system to ensure all residues are removed.
b. Inspect the Rollers:
Check the rollers for signs of wear, such as cracks, flat spots, or uneven surfaces. Damaged rollers can affect coating quality and should be replaced promptly.
Ensure the rollers are properly aligned and adjusted to maintain consistent coating thickness.
c. Clean the Coating Pan and Feed System:
Empty and clean the coating pan to prevent dried or hardened coating material from contaminating future batches.
Flush the feed system (pumps, hoses, and nozzles) with cleaning solvent to remove any residual coating material.
d. Check for Leaks:
Inspect the equipment for any leaks in the coating material or cleaning solvent lines. Address any leaks immediately to prevent material waste and equipment damage.
e. Lubricate Moving Parts:
Apply lubricant to moving parts, such as bearings and gears, to reduce friction and prevent wear. Use lubricants recommended by the equipment manufacturer.
2. Weekly Maintenance
Weekly maintenance involves more thorough inspections and cleaning to address issues that may not be apparent during daily checks.
a. Deep Clean the Rollers:
Remove the rollers from the machine and soak them in a cleaning solution to dissolve any hardened coating material.
Use a soft brush to scrub the rollers gently, ensuring all residues are removed. Rinse and dry them thoroughly before reinstalling.
b. Inspect and Clean the UV Curing System (if applicable):
Check the UV lamps for any signs of damage or reduced intensity. Replace lamps as needed to ensure proper curing.
Clean the reflectors and lenses in the UV curing chamber to maintain optimal light output.
c. Check the Conveyor System:
Inspect the conveyor belts for wear, tears, or misalignment. Clean the belts to remove any coating material buildup.
Ensure the conveyor system is running smoothly and adjust the tension if necessary.
d. Inspect Electrical Components:
Check electrical connections, switches, and controls for any signs of wear or damage. Tighten loose connections and replace faulty components.
3. Monthly Maintenance
Monthly maintenance focuses on preventive measures to avoid major breakdowns and ensure long-term performance.
a. Replace Worn Parts:
Replace any worn or damaged parts, such as rollers, bearings, seals, and belts. Keeping spare parts on hand can minimize downtime.
b. Calibrate the Equipment:
Calibrate the roller coating machine to ensure accurate coating thickness and consistent performance. Follow the manufacturer’s guidelines for calibration procedures.
c. Inspect the Frame and Structure:
Check the machine’s frame and structural components for signs of wear, rust, or damage. Address any issues to maintain the equipment’s stability and safety.
d. Test Safety Features:
Verify that all safety features, such as emergency stop buttons, guards, and sensors, are functioning correctly.
4. Seasonal or Annual Maintenance
Seasonal or annual maintenance involves a comprehensive inspection and servicing of the equipment.
a. Perform a Full System Flush:
Flush the entire coating system, including pumps, hoses, and nozzles, to remove any buildup or blockages.
b. Inspect and Replace Major Components:
Inspect major components, such as motors, pumps, and control systems, for signs of wear or damage. Replace any components that are nearing the end of their lifespan.
c. Check for Software Updates (if applicable):
If the roller coating machine is equipped with software or digital controls, check for updates or upgrades that can improve performance or add new features.
d. Schedule Professional Servicing:
Consider hiring a professional technician to perform a thorough inspection and servicing of the equipment. They can identify and address issues that may not be apparent during routine maintenance.
5. Best Practices for Optimal Performance
Use High-Quality Coatings: Low-quality coatings can cause buildup and clogging, leading to more frequent cleaning and maintenance.
Train Operators: Ensure operators are trained in proper equipment operation, maintenance, and cleaning procedures.
Keep a Maintenance Log: Maintain a log of all maintenance activities, including cleaning, part replacements, and inspections. This helps track the equipment’s performance and identify recurring issues.
Follow Manufacturer Guidelines: Always refer to the equipment manufacturer’s guidelines for maintenance and cleaning procedures to avoid voiding warranties or causing damage.
Proper maintenance and cleaning of roller coating equipment are essential for ensuring optimal performance, extending the equipment’s lifespan, and maintaining high-quality finishes. By following a regular maintenance schedule and adhering to best practices, manufacturers can minimize downtime, reduce repair costs, and achieve consistent, high-quality results. Whether it’s daily cleaning, weekly inspections, or annual servicing, a proactive approach to equipment maintenance will pay dividends in the long run.
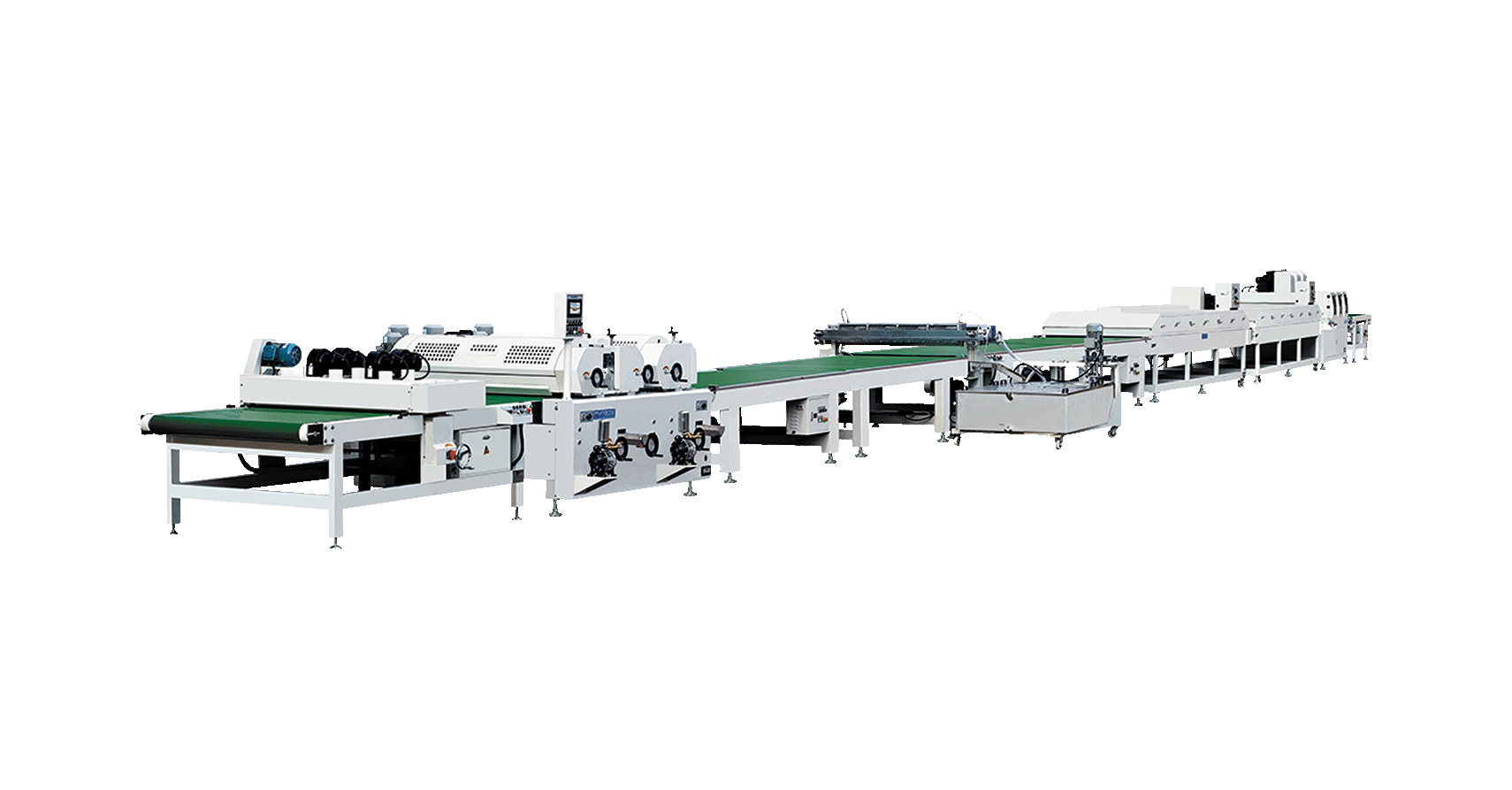


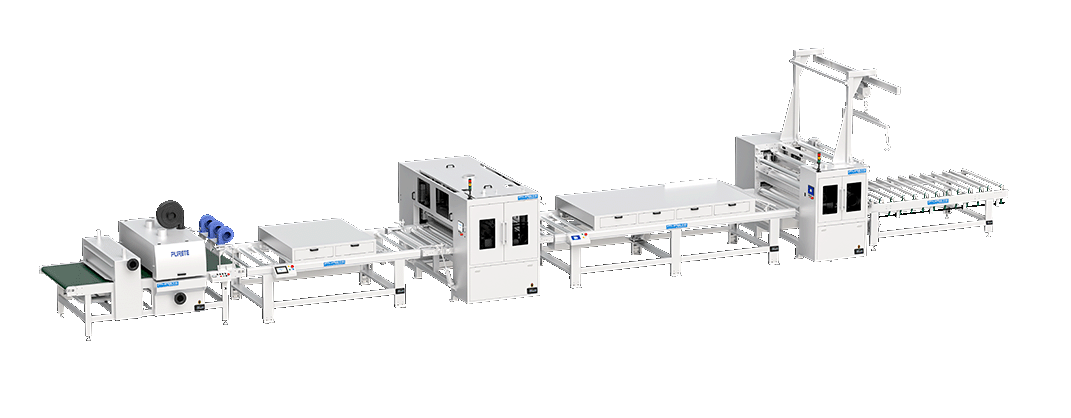
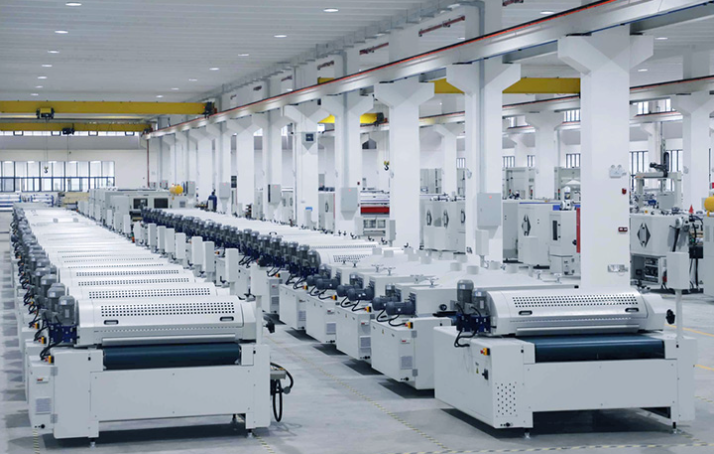
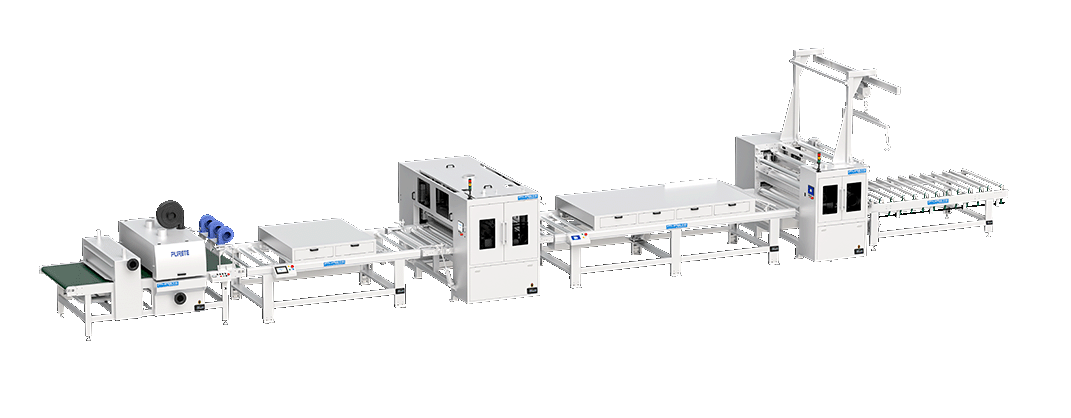
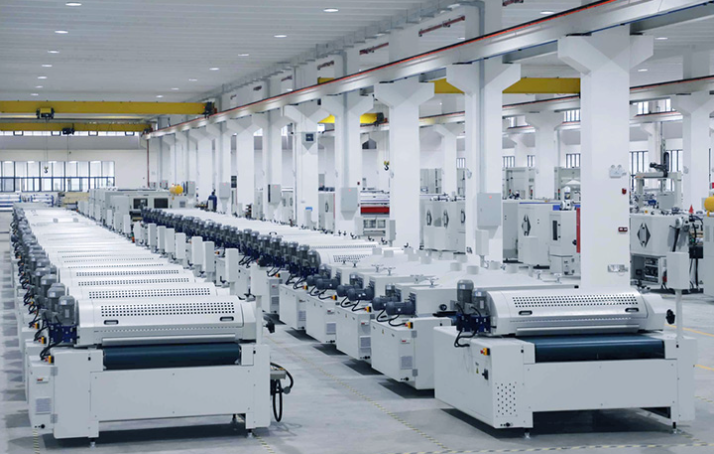
